نقش عمق فروبری محیط های دمایی در کالیبراسیون دماسنج ها
Technical Note: tfv-Temperature 001-00
محسن جزمی - خرداد 1400
مقدمه:
یکی از مهمترین عوامل بروز خطا در اندازه گیری دما توسط انواع حسگرهای دما و کالیبراسیون آنها در انواع محیط های دمایی ، عمق فروبری[1] دماسنج در منطقه حرارتی تحت اندازه گیری در کاربرد مورد نظر یا محیط دمایی کالیبراسیون است. اما فقط دانستن مقدار عمق فروبری محیط دمایی و قراردادن بخش حسگر وسیله اندازه گیری دما درآن نقطه یا منطقه کفایت نمی کند و باید الزامات مهم دیگری از جمله رعایت نسبت قطر وسیله اندازه گیری دما (شامل حسگر ، پوشش غلاف ، عایق بندی ) به قطر دهانه بخشی که دماسنج در آن فروبرده می شود (چاهک[2]) را مد نظر قرار داد تا خطای اندازه گیری دما و عدم قطعیت آن به حداقل برسد. معمولآ سازندگان محیط های دمایی کالیبراسیون (حتی سازندگان معتبر و شناخته شده ) در بخش مشخصات فنی کتابچه محیط دمایی کالیبراسیون، فقط به مقدار طولی عمق فروبری اشاره می کنند و با فرض اینکه استفاده کننده از آن رعایت الزامات فنی مرتبط با کمینه عمق فروبری را می کند ، به بیان مشخصات فنی مانند درستی نمایش دما ، پایداری[3] ، یکنواختی[4] ، پسماند دمایی[5] و اثر بارگذاری[6] اکتفا می کنند .
با این پیش فرض ، معمولأ عدم قطعیت عدم یکنواختی محوری گزارش شده در کتابچه مشخصات فنی محیط های دمایی در حد چند دهم درجه سلسیوس می باشد (معمولآ کمتر از 0.5 درجه سلسیوس در دماهای بالا) که با آنچه در عمل در صورت عدم رعایت تمام الزامات مرتبط با عمق فروبری دماسنج ها رخ می دهد تفاوت فاحش دارد و در ادامه ملاحظه خواهید کرد که این عدم قطعیت می تواند به بیش از 1% هم برسد که در دماهای بالا مقدار بزرگی خواهد شد ، بطور مثال در 1000 درجه سلسیوس با فرض عدم قطعیت 1% ، مقدار عدم قطعیت عامل عمق فروبری 10 درجه سلسیوس خواهد شد که مقدار بزرگی است.
خطا و عدم قطعیت فروبری و کاهش آن به عوامل زیادی بستگی دارد ، که مهمترین آتها عبارتنداز:
- انتخاب نوع محیط دمایی ،
- بازه دمایی کالیبراسیون ،
- ساختار دما سنج و نوع حسگرهای تحت کالیبره و حسگر مرجع مورد استفاده ،
- ضرایب انتقال حرارتی[7] و هدایت حرارتی[8] اجزای استفاده شده در محیط دمایی،
- سیم ها و سایر اجزای حسگر .
عواملی که معمولأ توسط کاربران محیط های دمایی مورد توجه قرار نمی گیرد و سازندگان نیز برای خراب نشدن مشخصات فنی خود، در کتابچه محیط دمایی آن را بصورت روشن ذکر نکرده و فقط به انتشار مقالات و نکات فنی پشتیبانی کننده در وبسایت خود برای رعایت کمینه عمق فروبری برای دماسنج های مختلفی می کنند که ممکن است کاربران معمولی از آن اطلاع نداشته یا توانایی محاسبه سهم عدم قطعیت فروبری را با توجه به مطالب منتشره در این نکات فنی نداشته باشند و در همان حال کالیبراسیون دما سنج ها و حسگرهای دمایی را انجام وخوشبینانه اریبی و عدم قطعیت های غیر واقعی به مشتریان خود گزارش کنند.
در یک دسته بندی بسیار کلی ، محیط های دمایی کالیبراسیون را می توان به دو دسته زیر تقسیم کرد:
- محیط دمایی خشک ( کوره های مجهز به بلوک های فلزی ، کوره های لوله ای)
- محیط دمایی سیال مایع /جامد( آب، روغن ، اتیلن گیکول ، پودر، نمک و ...)
سه مشخصه یا خصوصیت مهم در محيط هاي دمايي کالیبراسیون عبارتند از :
- پايداري: معياري براي ثابت بودن دما نسبت به مروز زمان (در کوتاه مدت يا بلند مدت)
- يکنواختي: معياري براي يکسان بودن دما در محل هاي فيزيکي مختلف محيط دمايي
- عمق فروبري : معياري براي امکان کاليبراسيون دما سنج ها با یا بدون ملحقات با طول ها و اقطار مختلف
یکنواختی دمایی محیط های کالیبراسیون در برگیرنده یکنواختی محوری[9] و یکنواختی شعاعی[10] است .یکنواختی محوری نقشی مهم در تعیین عمق فروبری و درستی اندازه گیری های دما بازی می کند ، ولی در تعیین عمق فروبری عوامل بسیار مهم دیگری نیز دخیل هستند که در این مطلب به آنها پرداخته می شود. یکنواختی محوری یعنی یکنواختی دما در فواصل عمودی مختلف از آخرین نقطه قرارگیری حسگر دمایی در محیط دمایی کالیبراسیون نسبت به دمای محیط پیرامون( بیرونی) یا بخش بالای محیط دمایی است که بخش انتهایی ساقه[11] حسگر و پایانه های آن از محیط دمایی خارج شده است .
معمولأ سازندگان برای کمک به تثبیت و یکنواختی دمایی و همچنین پیش بینی محلی برای قرار دادن دماسنج ها در محیط دمایی کالیبراسیون خشک از بلوک های فلزی سوراخ شده با قطرهای مختلف و تا عمق مناسب استفاده می کنند. این بلوک های فلزی بسته به بازه و بیشینه دما ممکن است جنس های مختلفی مانند برنز، آلومینیوم و فولاد آلیاژی داشته باشند و معمولآ آنها را با نام جاساز[12] می شناسند و به سوراخ های آن چاهک اطلاق می شود. این بلوک ها به دلیل جرم سنگین تری که نسبت به سایر اجزای محیط دمایی دارند ، می تواند حرارت را براحتی از گرم کننده های محیط دمایی دریافت ، علاوه بر انتقال به حسگر ، انرژی حرارتی را در خود حفظ نمایند و باعث تثبیت دمایی بهتر این محیط ها بشوند.
دسته دیگری از محیط های دمایی کالیبراسیون ،از سیال مایع یا جامد مانند روغن ، اتیلن گلیکول ، آب یا حتی پودر و نمک استفاده می کنند تا انتقال حرارت بین گرم کن ها و دماسنج ها به راحتی انجام شود و از همزن تعبیه شده در آنها برای ایجاد همگنی و یکنواختی دما استفاده می کنند. بدیهی است همزن ها همزن ها وظیفه برقراری همگنی و یکنواختی (محوری و شعاعی) در کل محیط دمایی کالیبراسیون را به عهده دارند.
بایستی یادآور شد که محیط های دمایی خشک برای کالیبراسیون دماهای بالا تا 1200 درجه سلسیوس (حتی 1300 درجه سلسیوس) و محیط های سیال مایع و پودر برای دماهای پایین تر از صفر درجه سلسیوس تا کم و بیش 350 نه درجه سلسیوس استفاده می شوند.
به دلیل اهمیت موضوع هدایت حرارتی دماسنج ها و تعیین کمینه عمق فروبری آنها در محیط های دمایی مورد استفاده برای مقاصد اندازه گیری و کالبیراسیون ، در ادامه این مقدمه موضوعات مختلفی در شش بخش زیر تشریح می شوند:
بخش اول ) هدایت ساقه و عمق فروبری
بخش دوم) مدل ریاضی برای تعیین کمینه عمق فروبري وخطای ناشی ازآن
بخش سوم )مشکلات موجود در تعیین درست عمق فروبری
بخش چهارم ) روش اجرایی تعیین کمینه عمق فروبری و ارزشیابی خطای هدایت ساقه
بخش پنجم ) عمق فروبری در کوره های کالیبراسیون خشک قابل حمل
بخش ششم ) عمق فروبری در اندازه گیری دما در نقاط ثابت دمایی
بخش اول ) هدایت ساقه و عمق فروبری
مطابق آنچه در مقیاس بین المللی دمایی ITS-90 در خصوص عمق فروبری بیان شده، یک دماسنج هنگامی به اندازه کافی فروبرده محسوب می شود که با فروبری بیشتر ازآن در محیط دمایی تثبیت شده ، تغییری در نشاندهی دمای آن به وجود نیاید. همچنین در استاندارد بین المللی ASTM D7962-2017 کمینه عمق فروبری بصورت زیر تعریف شده است :
"عمقی است که وقتی یک دماسنج در یک محیط با دمای یکنواخت فروبرده می شود ، چنانچه مقدار فروبری آن افزایش یابد، تغییری در نشاندهی دما بیش از رواداری مشخص شده ایجاد نشود ."
ساقه دماسنج بخشی از دماسنج بین حسگر داخلی و سیم های رابط خروجی آن است و هدایت حرارتی در طول آن را باعث می شوند. بنابراین خطای فروبری تقریبأ نتیجه هدایت حرارتی ساقه دماسنج (ها) است. این موضوع وقتی رخ می دهد که دمای منبع حرارتی با دمای پایانه دماسنج در قسمت دستگیره یا کابل انتهایی آن متفاوت باشد. بطور مثال در یک ترموکوپل ، اختلاف دمای بین نقطه اتصال گرم با اتصال سرد باعث ایجاد هدایت حرارتی در تمام طول زوج سیم ترموکوپل و حتی پوشش محافظ آن خواهد شد. این اختلاف دمایی و هدایت حرارتی برقرار شده در طول ساقه دماسنج ، باعث بروز اختلاف در دمای قرائت شده توسط حسگر و دمای واقعی منبع حرارتی می شود.
فرض کنید یک محیط دمایی کالیبراسیون مجهز به بلوک فلزی سوراخ دار برای تثبیت دمایی و کالیبراسیون حسگر های دما است و یک دماسنج مرجع و یک دماسنج تحت کالیبره در سوراخ های آن با عمق یکسان قرار داده شده اند . با وجود اینکه هردو دماسنج، دمای تثبیت شده یکسانی را تجربه می کنند ، وقتی پدیده هدایت حرارتی در طول ساقه دماسنج تحت کالیبره و دماسنج مرجع اتفاق بیافتد ، بین دمای بلوک فلزی و دمای نشان داده شده توسط دماسنج تحت کالیبره اختلاف خواهد بود و همچنین بین دمای بلوک فلزی و دمای اندازه گیری شده توسط دماسنج مرجع نیز اختلاف مشابه ای (ولی نه حتما برابر با آن) پیش خواهد آمد.در هرصورت هیچیک از دماسنج ها، دمای درست بلوک فلزی (دمای یکنواخت محیط دمایی کالیبراسیون) را قرائت نمی کنند. ازعلت این اختلاف دمایی به عنوان عامل عمق فروبری و هدایت ساقه نامبرده می شود .
دو دماسنج که کنار همدیگر در یک عمق در یک محیط دمایی یکنواخت (هم دما) قرارداشته باشند و دمای یکسانی را تجربه کنند، ولی اگر ساقه های آنها از مواد مختلف ساخته شده باشند ، دو دمای مختلف را قرائت خواهند کرد. در حالت قبل اگر جنس ساقه دماسنج تحت کالیبره با جنس ساقه دماسنج مرجع متفاوت باشند، حتی اگر کنار یکدیگر و در عمق یکسان قرار گرفته باشند، بین قرائت های آنها اختلاف خواهد بود ، زیرا ممکن است عمق قرارگرفته برای هردو آنها عمق مناسب برای فروبری نباشد. توجه داشته باشید این اختلاف دمایی ، غیر از اختلاف بین دمای واقعی ب محیط دمایی کالیبراسیون و دمای قرائت شده است. بطور مثال دو دماسنج یکی با غلافی از جنس اینکونل و دیگری با غلافی از جنس کوارتز که طول و قطر یکسان دارند و هردو کنار هم در یک عمق فروبری در یک محیط دمایی برای کالیبراسیون قرار داده می شوند ، بدلیل پدیده هدایت حرارتی و نیاز به کمینه عمق فروبری غیر یکسان ، دماهای مختلفی هر چند با اختلاف کم را قرائت خواهند کرد.
حتی اگر ساقه دما سنج ها جنس یکسان داشته باشند، بازهم به دلیل تفاوت در ساختار فیزیکی و ابعاد ، به خصوص تفاوت در موقعیت قرارگیری و طول بخش حسگر دماسنج ها و تفاوت در قطر و طول ساقه می توانند دماهای متفاوت از هم را قرائت کنند ، که این اختلاف هم به دلیل پدیده هدایت حرارتی و کمینه عمق فروبری مورد نیاز متفاوت آنها پیش می آید.
بایستی یادآور شد که دماسنج ها، دمای میانگین در طول بخش حسگری خود را اندازه می گیرند ،به همین دلیل طول این بخش و موقعیت قرارگیری آن در ساختار دماسنج نقش تعیین کننده ای در اختلاف دما با دمای بلوک فلزی و همچنین تعیین عمق فروبری دارد. بصورت سرانگشتی هرچه اختلاف بین طول حسگر، قطر و طول ساقه دماسنج ها بیشتر باشد، اختلاف دمای قرائت شده بیشتری بدلیل پدیده هدایت حرارتی خواهد بود و لازمست برای کاهش اثر این عامل ، عمق فروبری مناسب برای این دماسنج ها تعیین و دماسنج ها در بزرگترین عمق فروبری تعیین شده قرارداده شوند تا اریبی و عدم قطعیت این عامل به حداقل برسد.
در حالیکه هدایت ساقه ، خصوصیت دماسنج (ها)است و نه خصوصیت محیط دمایی کالیبراسیون ، ولی عمق فروبری خصوصیتی مرتبط با هر دو آنها ست . در حالت ایده آل هنگامی که تمامی دماسنج ها به اندازه کافی درون بلوک فلزی فروبرده شوند و درنتیجه خطای ناشی از هدایت ساقه قابل صرف نظر خواهد بود.
بنابراین نکته کلیدی برای غلبه برعامل هدایت ساقه ، عمق فروبری کافی دماسنج های مرجع و تحت کالیبره است .
به صورت کلی عوامل تاثیر گذار بر خطاها و عدم قطعیت ناشی از هدایت حرارتی از طریق دماسنج عبارتند از:
- ضریب هدایت حرارتی (جنس ساقه و اجزای دیگر) : K
- سطح مقطع : A
- اختلاف دمایی بین منبع حرارتی و دمای پیرامون: Delta-T
- عمق فروبری: L
الف) ضریب هدایت حرارتی (جنس ساقه و اجزای دیگر) : K
هرچه مقاومت حرارتی اجزای دماسنج و ساقه آن بیشتر باشد، هدایت و انتقال حرارت به محیط بیرون یا دریافت حرارت ازآن کمتر خواهد بود . نوع ماده (جنس) و قطر سیم های حسگر ، ضخامت پوشش محافظ (غلاف حسگر) و موادی که درساخت آن بکار رفته،تمامی در ضریب هدایت حرارتی تاثیر گذارند. هرچه دیواره غلاف ضخیم تر باشد، هدایت حرارتی بیشتر و خطا نیز افزایش پیدا خواهد کرد.
ب) سطح مقطع : A
صرف نظر از ضریب هدایت حرارتی جنس ساقه دماسنج ، هرچه سطح مقطع ساقه بزرگتر باشد ، خطا بزرگتر خواهد بود و برای جبران نیاز به عمق فروبری بیشتر خواهد بود. نسبت قطر ساقه حسگر (D) به عمق فروبری پیش بینی شده در محیط دمایی کالیبراسیون (L) ، نسبت تعیین کننده ای در کاهش اثر این خطا می باشد (D/L). برای مثال کالیبراسیون دما سنج ها با طول کوتاه و با قطر بزرگ (مانند دماسنج های عقربه ای و سوئیچ های دما) برای دستیابی به درستی های بالا بدلیل غالب شدن اثر عامل هدایت حرارتی برسایر عوامل تاثیر گذار بر عدم قطعیت کالیبراسیون دما ،چالش برانگیز است.
وقتی از محیط های دمایی خشک مانند کوره های مجهز به بلوک فلزی سوراخ دار به عنوان محیط کالیبراسیون استفاده می شود ، قطر و سطح مقطع موثر (Deff) متفاوت با قطر و سطح مقطع دماسنج (D) و بزرگتر ازآن می باشد ،زیرا انتقال و هدایت حرارتی در حالتی که فیلمی از هوا بین بلوک فلزی و حسگر ها بوجود می آید با حالتی که مانند محیط های دمایی سیال مایع که تماس کامل بین سیال مایع و حسگرها وجود دارد متفاوت است. این موضوع وقتی اندازه گیری یا کالیبراسیون بخواهد در خلأ، انجام شود، بدلیل اینکه انتقال حرارت فقط بصورت تابشی[13] است و نه هدایتی (رسانشی[14]) ، پیچیده تر و قطرو سطح مقطع موثر بسیار بزرگتر از سطح مقطع دماسنح ها خواهد بود.
پ ) اختلاف دمایی بین منبع حرارتی و دمای پیرامون: Deta-T
هرچه اختلاف دمایی محیط کالیبراسیون به عنوان منبع حرارتی با دمای محیط پیرامون آن به خصوص در محل پایانه های دماسنج که وسیله اندازه گیری دما و ملحقات آن قراردارند بیشتر باشد، هدایت حرارتی و درنتیجه خطاهای ناشی ازآن بزرگتر و به عمق فروبری بیشتر برای جبران این خطا ها و کاهش عدم قطعیت آنها نیاز است. اختلاف دمایی بین منبع حرارتی و دمای محیط پیرامون را در محیط های کالیبراسیون دمایی مجهز به بلوک فلزی که دمایی تثبیت شده دارد، می توان به اختلاف دمای این بلوک و دمای محیط تفسیر کرد و حسگر دمایی ، دمای این بلوک را اندازه گیری می کند. معمولأ کالیبراسیون حسگرهای دما در بازه وسیعی از دما و در دماهای مختلف دراین بازه انجام می شود . بنابراین انتظار می رود در نقاط دمایی مختلف کالیبراسیون ، به عمق فروبری های مختلفی نیاز باشد و هرچه دمای نقطه کالیبراسیون افزایش پیدا کند، خطاهای مرتبط با هدایت حرارتی بزرگتر و درنتیجه به عمق فروبری بیشتری نیاز باشد. البته پیوست مدرک معتبر بین المللی منتشره از طرف BIPM در خصوص مقیاس بین المللی دما ITS-90 ، در این خصوص به نکته ای مهم اشاره دارد و آن اینست که معمولآ عمق فروبری مورد نیاز برای کالیبراسیون حسگر های دمایی تا دمای حدود 500 درجه سلسیوس افزایش پیدا می کند و پس ازآن کاهش جزئی پیدا کرده و ثابت می ماند. دلیل آن را هم غالب شدن انتقال حرارتی از طریق پدیده تابش حرارتی در مقابل هدایت حرارتی از طریق ساقه دماسنج می داند . با مدنظر قراردادن این نکته، می توان کمینه عمق فروبری برای محیط های دمایی کالیبراسیون خشک مانند کوره های مجهز به بلوک های فلزی را در دمای بین 400 تا 500 درجه سلسیوس تعیین و ازآن برای دماهای بالاتر که مناسب برای کالیبراسیون ترموکوپل های صنعتی به خصوص نوع K ، R ، Sو حتی B است استفاده کرد.
ت) عمق فروبری: L
عوامل بیان شده در بالا که در خطا و عدم قطعیت در کالیبراسیون دمای انواع دماسنج ها درمحیط های دمایی بدلیل عامل هدایت حرارتی ساقه دماسنج ها تاثیر گذارند را نمی توان در اغلب مواقع براحتی و بسادگی کنترل کرد ، ولی درعوض از طریق عمق فروبری براحتی می توان این مهم را به انجام رساند. با افزایش عمق فروبری، اثر تمامی عوامل بالا در افزایش خطا و عدم قطعیت عامل هدایت ساقه را می توان جبران کرد. برای دستیابی به بالاترین درستی ، بایستی دماسنج های تحت کالیبره و مرجع را در حالیکه کمترین فاصله از همدیگر رادارند، در بیشترین عمق فروبری ممکن قرار داد . در برخی موارد خاص که دماسنج تحت کالیبره و دماسنج مرجع به کمینه عمق های فرو بری های متفاوت نیاز داشته باشند ، بطور مثال بدلیل تفاوت در طول بخش حسگرشان یا تفاوت در قطر و سطح مقطع ، آنها را می توان بارعایت شرط کمینه عمق فروبری مورد نیاز هریک و درحالیکه نزدیک هم قرارداده می شوند کالیبره (مقایسه) کرد، بطور مثال در یک سوراخ (چاهک) از بلوک فلزی در محیط های خشک یا به صورت به هم چسبیده در محیط های سیال مایع قرار داد.
نکته: رابطه بین خطا و عدم قطعیت ناشی از هدایت ساقه و محدودیت درعمق فروبری و عوامل فوق ، بصورت مدل های معتبر ریاضی ساده و پیچیده استخراج و ارائه شده است که درادامه این مطلب به مدل ریاضی ساده آن برای محیط های دمایی خشک و سیال مایع یا پودر مجهز به همزن پرداخته خواهد شد. در خصوص مدل ریاضی پیچیده نیز در قالب یک مطلب جداگانه با عنوان "تحلیل خطای فروبری در مورد ترموکوپل ها "پرداخته شده که علاقمندان می توانند به آن مراجعه نمایند.
بخش دوم ) مدل ریاضی برای تعیین کمینه عمق فروبري وخطای ناشی ازآن
چون دماسنجها بطور كامل در محيط دمائي مورد نظر فرو برده نمي شوند ، مسئله فروبري در اغلب اندازه گيريهاي دما وجود دارد . ساقه دماسنج ، غلاف و سيم هاي رابط مسيري براي جريان پيوسته گرما بين محيط دمائي و دنياي بيرون ايجاد مي كنند. به خاطر همين جريان حرارتي ، دماي حس شده توسط نوك دماسنج با دماي محيط دمائي كه درآن قرار دارد متفاوت است .
شکل 1، نمودار تغییرات دمایی تقریبی و جریان حرارتی شکل گرفته در طول ساقه یک دماسنج نوعی وقتی در یک محیط دمایی قرار می گیرد را نشان می دهد. معمولأ پروفایل دمایی شکل گرفته در طول دماسنج بصورت پیوسته با آن تغییر می کند. انتهای گرم دماسنج نزدیک به دمای محیط دمایی و منبع حرارتی است ،درحالیکه انتهای سرد دمایی نزدیک دمای محیط پیرامون وبیرونی دارد. فرض کنید بخش پایینی و نوک دماسنج ،درون محیط دمایی حاوی سیال درحال هم زدن (مانند حمام های کالیبراسیون آب یا روغن مجهز به همزن) احاطه شده است و بایستی انتقال حرارت به دماسنج انجام تا اتلاف حرارتی توسط ساقه دماسنج را جبران کند. این تبادل و انتقال حرارتی که درلایه های مرزی دور دماسنج و سطح حسگر رخ می دهد ، به این معنی است که نوک دماسنج یا حتی بخش حسگری آن هنوز به دمای محیط دمایی (Tm) نرسیده و تعادل حرارتی برقرار نشده است. بایستی توجه داشت که جریان حرارتی در طول دماسنج به گرادیان دمایی در طول دماسنج دارد وهرچه دماسنج بیشتر داخل محیط دمایی باشد ،این جریان حرارتی کمتر خواهد بود.
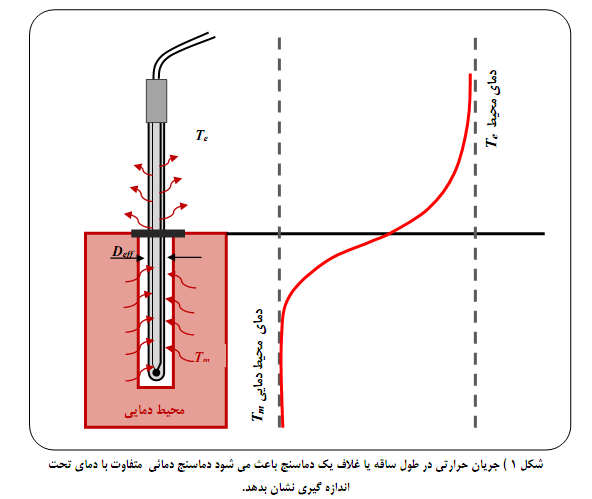
درکتاب "دمای قابل ردیابی" که نویسنده آن نیکلاس و وایت هستندو توسط آزمایشگاه استاندارد نیوزیلند منتشر شده و نوشته ای وزین در خصوص کالیبراسیون دما به حساب می آید ، مدل ریاضی ساده ای برای این جریان حرارتی شکل گرفته در دماسنج به خصوص در محدوده نوک آن که درون محیط دمایی حاوی سیال درحال هم زدن (مانند حمام های کالیبراسیون آب یا روغن مجهز به همزن) ارائه شده است . در این مدل، خطاي ناشي از عمق فروبري نامناسب( Delta-Tims ) بستگي به اختلاف دماي سيستم تحت اندازه گيري(Tm) و دماي محيط اطراف (Te) ، مقدار عمق فروبري (L) و قطر مؤثر دماسنج (Deff) دارد و ازرابطه زیر تبعيت ميکند :
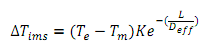
که در رابطه فوق K ضريبي ثابت با مقدار تقريبي مساوي ولي کمتر از يک است .هردو مقدارK و Deff به مقاومت دمایی[15] بين دماسنج و محیط دمایی که درآن قرارداده شده و به ظرفيت حرارتی[16] دماسنج و محیط دمایی بستگی دارند.
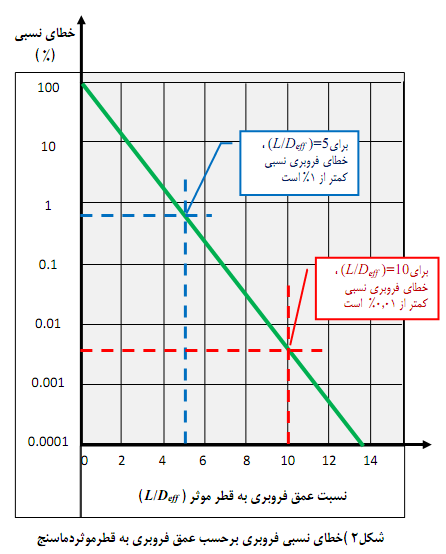
که در رابطه فوق K ضريبي ثابت با مقدار تقريبي مساوي ولي کمتر از يک است .هردو مقدارK و Deff به مقاومت دمایی[15] بين دماسنج و محیط دمایی که درآن قرارداده شده و به ظرفيت حرارتی[16] دماسنج و محیط دمایی بستگی دارند.
این معادله که شکل ترسیم شده آن در مقیاس لگاریتمی برای K=1 را می توان در شکل 2 مشاهده کرد، برای تعیین کمینه عمق فروبری که تضمین می کند، خطای ناشی از هدایت حرارتی دماسنج قابل صرف نظر است بسیار مفید و کاربردی است. همچنین با استفاده ازآن برای سطح درستی و یا عدم قطعیت هدف، می توان کمینه عمق فروبری را تعیین کرد.
در مورد قطر موثر دماسنج (Deff) بایستی اذعان داشت که برای محیط های دمایی سیال مجهز به همزن مانند حمام های آب ، روغن و پودرسیال می توان به درستی آنرا با قطر بیرونی دماسنج (D) یکسان و برابر فرض کرد (Deff=D) ، درحالی که در خصوص محیط های دمایی خشک به اینصورت نیست و درادامه توضیحات تکمیلی ارائه خواهد شد.
همانطور از معادله فوق و نمودار شکل 2 مشهود است ، هر چه عمق فروبري دما سنج بيشتر باشد ، خطاي نسبی ناشي از آن كوچكتر ميشود.خطای نسبی در شکل 2 از رابطه زیر بدست می آید :

برای برآورد عدم قطعیت ناشی از هدایت حرارتی ساقه دماسنج و بعبارت دیگر عدم قطعیت عمق فروبری ، کافی است خطای عمق فروبری Delta-Tims را به عنوان بیشترین بازه تغییرات دمایی ناشی از هدایت ساقه درنظر گرفت و با تقسیم آن بر مقسم 2 ، حدبالا و پایین عدم قطعیت این عامل ( ± a ، بازه تغییرات توزیع مستطیلی) را تعیین کرد . با فرض توزیع مستطیلی برای این عامل ، کافی است آنرا بر مقسم توزیع مستطیلی (رادیکال3) تقسیم کرد تا عدم قطعیت استاندارد این عامل برآورد شود:
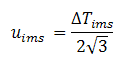
بطور مثال برای خطای عمق فروبری به اندازه 0.3 درجه سلسیوس ، عدم قطعیت استاندارد عمق فروبری خواهد شد:
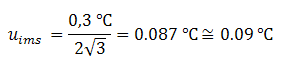
با توجه به جزئیات ترسیم شده در نمودار شکل 2 ،و همچنین توصیه سازندگان محیط های دمایی کالیبراسیون و حسگرهای دمایی و منابع معتبر مختلف ، معمولآ قواعد ساده زیر را برای تعیین عمق فروبری مناسب دماسنج ها توصیه می کنند. فقط باید به این نکته کلیدی توجه داشت که این توصیه ها برای وقتی است که بتوان قطر موثر دماسنج را با قطر بیرونی آن یکسان درنظر گرفت (Deff=D) ، مانند وقتی از محیط های دمایی سیال مایع یا پودر مجهز به همزن استفاده می شود:
- برای اندازه گیری های صنعتی دما با درستی نسبی حدود 1% ، کمینه عمق فروبری معادل 5 برابر قطر ساقه حسگر به علاوه طول بخش حس کننده داخلی (5D+SL)
- برای کالیبراسیون حسگرهای دما در آزمایشگاه های خوب با درستی نسبی 0.01% ، 10 برابر قطر ساقه به علاوه طول بخش حس کننده (10D+SL) برای کالیبراسیون حسگر های دما در سطح درستی نسبی تا 0.0001%
- در آزمایشگاه های کالیبراسیون سطح مرجع و اندازه گیری ها در نقاط ثابت دمایی ، 15 برابر قطر ساقه حسگر (15D+SL)
- برای کالیبراسیون حسگرهایی مانند SPRT که عدم قطعیت بسیار پایین دارند کمینه عمق فروبری بین 20 تا 30 برابر قطر ساقه حسگر(20 to 30D +SL)
- برخی منابع نیز برای رفع هرگونه شبهه برای تمامی دماسنج ها، کمینه عمق فروبری مورد نیاز برای حذف خطاهای مرتبط با هدایت حرارتی ساقه حسگر را 20 برابر قطر ساقه به علاوه طول حسگر را توصیه می کنند
که D قطر بیرونی ساقه دماسنج و SL طول بخش حس کننده یا همان طول حسگر داخلی است.
براساس توصیه های فوق، بطور مثال برای کالیبراسیون یک حسگر مقاومت پلاتینی صنعتی (IPRT) با قطر 7 میلی متر و طول بخش حس کننده 29 میلی متر ، در یک محیط دمایی سیال مایع ، کمینه عمق فروبری 134 میلی متر می باشد. (15 برابر قطر ساقه + طول حسگر)
البته روابط بالا با این پیش فرض است که نوک بخش حسگر دما در پایین ترین بخش ساقه دماسنج باشد.اگر محل نوک بخش حسگر بالاتر از پایین ترین بخش ساقه دماسنج باشد ، بایستی این فاصله نیز به طول استخراج شده از نمودار شکل 2 اضافه شود. بنابراین قبل از شروع به کالیبراسیون دماسنج ها ، بایستی اطلاعاتی در مورد نوع حسگر، محل دقیق سر ، نقطه اتصال و طول بخش حس کننده دماسنج که درون ساقه حسگر دما جاسازی شده است وجود داشته باشد یا از سازنده، مشخصات فنی منتشره و ... این اطلاعات مهیا تا با انتخاب عمق فروبری مناسب ، خطا و عدم قطعیت اندازه گیری ها و کالیبراسیون را به حداقل مقدار و بازه اطمینان ممکن کاهش داد.
دربرخی موارد ممکن است بتوان درعمل دمای محیط دمایی و قطر موثر را از اندازه گیری های متوالی در عمق های فروبری مختلف برآورد کرد .دراین خصوص در کتاب " دمای قابل ردیابی" تکنیکی برای محاسبه دمای محیط دمایی (Tm) و قطر موثر (Deff) ارائه شده است که کاربردی است.
بطور مثال فرض کنید سه اندازه گیری در عمق های فروبری L1 ، L2 و L3 با فواصل مساوی (L2-L1=L3-L2=Delta-L) انجام و دماهای خوانده شده به ترتیب T1 ، T2 و T3 باشند. با استفاده از رابطه کلی زیر :
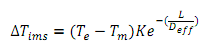
و انجام عملیات ریاضی و برونیابی می توان اثبات کرد که دمای محیط دمایی(Tm) و قطر موثر دماسنج (Deff) از روابط زیر به دست می آیند :
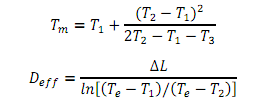
بدیهی است که به دلیل برون یابی ، عدم قطعیت نتایج فوق می تواند مورد پرسش باشد.
مثال : سه اندازه گیری دمایی در عمق های فروبری 3 ، 4 و 5 سانتی متری (از سطح بالای محیط دمایی) انجام و به ترتیب دماهای 115 ، 119 و 121 درجه سلسیوس خوانده می شود. دمای محیط دمایی و قطر موثر دماسنج را حساب کنید.
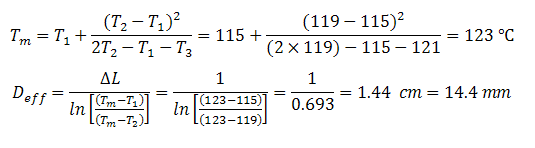
بخش سوم )مشکلات موجود در تعیین درست عمق فروبری
معمولأ برآورد درست کمینه عمق فروبری براساس رابطه بیان شده بالا با سه مشکل روبروست :
- قطر موثر دماسنج (Deff) به خصوص در محیط های خشک دمایی ،
- موقعیت و طول بخش حسگر دماسنج ،
- استفاده از غلاف های تودر تو یا چاهک دمایی[17] ،
الف) قطر موثر دماسنج (Deff) در محیط های خشک دمایی
در تعیین عمق فروبری براساس معادله ارائه شده دربالا، مشکل اصلی مقادیر نامعلوم K و Deffهستند که به محیط اطراف و سیالی که دما سنج را احاطه کرده و به خود دماسنج بستگی دارند. این رفتار متغیر T ناشی از هدایت های حرارتی و ظرفیت های حرارتی متفاوت در سیستم های اندازه گیری و کالیبراسیون دما با استفاده از محیط های دمایی است.
برای حالتی که محیط دمایی بخوبی همزده می شود ، مانند حمام های آب ، روغن یا پودرسیال مجهز به همزن، معادله مزبور با برابر فرض کردن قطر موثر دماسنج (Deff) و قطر بیرونی دماسنج (D) بخوبی جواب می دهد (Deff = D). ولی برای حالتی که محیط دمایی به همزن مجهز نیست ، مانند محیط های دمایی خشک، مقاومت دمایی اضافه ای ناشی از لایه های مرزی در سیال بوجود می آید .این موضوع باعث می شود قطر موثر بسیار بزرگتر از قطر واقعی دماسنج باشد.
در موضوع عمق فروبری ، هنگامی که اندازه گیری دما در حضور هوا ، سیال گازی یا حتی خلأ انجام می گیرد ، قطر موثر دماسنج ها ممکن است بیش از 10 برابر قطر واقعی آن باشد، طوری که برای دماسنجی که برای کالیبراسیون آن در حمام های کالیبراسیون آب یا روغن به عمق فروبری 10 برابر قطر آن نیاز است، برای اندازه گیری دما در محیطی که هوا یا فیلمی از هوا وجود دارد ،در حالت بدبینانه نیاز به عمق فروبری 100 برابری است. علت این مشکل عمده اثرات لایه های مرزی بین سطح بیرونی بخش حسگر و غلاف (ها) و به خصوص لایه مرزی بین سطح بیرونی دماسنج و سطح داخلی چاهکی است که دماسنج برای اندازه گیری دما یا کالیبراسیون دماسنج ها درآن قرارداده می شود و معمولآ با هوا یا فیلمی ازآن پر شده است می باشد. این لایه های مرزی ، مقاومت دمایی بین دماسنج و هوا را بسیار بیشتر از وقتی از سیال همزده (مانند حمام های مایع) استفاده می شود، افزایش می دهد .
براساس تحقیقات وارزیابی هایی که طی چند سال برروی انواع محیط های دمایی خشک مجهز به بلوک های فلزی سوراخ دار در آزمایشگاه سطح اول دما در شرکت Isotech آلمان برروی محصولات خود و دردماهای مختلف انجام داده و منتشر کرده است ، اثبات شده است که برای این محیط های دمایی خشک که یک فاصله هوایی بین دماسنج و چاهک بلوک فلزی آن وجود دارد ، می توان از همان رابطه قبلی که متعلق به محیط های دمایی سیال مجهز به همزن است ،برای تعیین عمق فروبری با توجه به سطح درستی مورد نظر استفاده کرد ، فقط کافی است قطر موثر (Deff)را دو برابر قطر بیرونی دماسنج تحت آزمون یا دماسنج مرجع درنظر گرفت (Deff=2D).
شکل 3 ، نمودار اصلاح شده شکل 2 را برای وقتی محیط دمایی ، محیط خشک است و فاصله هوایی بین دماسنج و چاهک قرار گرفته درآن وجود دارد را نشان می دهد. دراین نمودار تنها محور افقی که نسبت عمق فروبری برحسب قطر موثر است تغییر کرده و مقیاس آن دو برابر شده است.
اغلب محیط های دمایی خشک مجهز به بلوکه های فلزی سوراخ دار که به عنوان کوره های کالیبراسیون خشک قابل حمل شناخته می شوند عمق فروبری حدود 150 میلی متر ( 15 سانتی متری) دارند و از نمودار شکل 3 می توان استنتاج کرد که هرچه قطر دماسنج تحت کالیبره یا مرجع افزایش پیدا کند ، به عمق فروبری بلندتری نیاز است یا بایستی درستی یا عدم قطعیت مورد نظر را کاهش داد. با توجه به شکل 3 ، با افزایش حدود 2.5 برابری قطر دماسنج (بطور مثال از 10L/D به 4L/D ) ، خطای نسبی از زیر 1% به حدود 10% افزایش پیدا می کند.
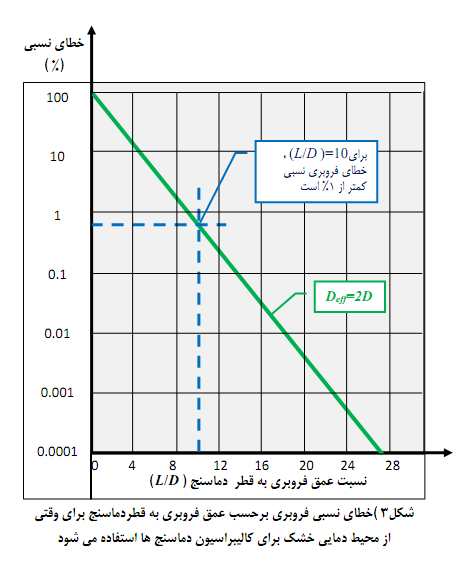
بنابراین مشابه قبل، براساس جزئیات ترسیم شده در نمودار شکل 3 ، برای تعیین کمینه عمق فروبری مورد نیاز برای کالیبراسیون دماسنج ها در محیط های دمایی خشک که Deff=2D فرض درستی است ، قواعد ساده زیر توصیه می شود:
- برای اندازه گیری های صنعتی دما با درستی نسبی حدود 1% ، کمینه عمق فروبری معادل 10 برابر قطر ساقه حسگر به علاوه طول بخش حس کننده / حسگر داخلی (10D+SL)
- برای کالیبراسیون حسگرهای دما در آزمایشگاه های خوب با درستی نسبی 0.01% ، 20 برابر قطر ساقه به علاوه طول بخش حس کننده (20D+SL)
- برای کالیبراسیون حسگر های دما در سطح درستی نسبی تا 0.0001% در آزمایشگاه های کالیبراسیون سطح مرجع و اندازه گیری ها در نقاط ثابت دمایی ، 30 برابر قطر ساقه حسگر (30D+SL)
که D قطر بیرونی ساقه دماسنج و SL طول بخش حس کننده یا همان طول حسگر داخلی است.
بطور مثال برای کالیبراسیون یک حسگر مقاومت پلاتینی صنعتی با قطر 7 میلی متر و طول بخش حس کننده 29 میلی متر ، در یک محیط دمایی خشک ، کمینه عمق فروبری 239 میلی متر نیاز است (30 برابر قطر ساقه + طول حسگر) که در مقابسه با وقتی از محیط دمایی با سیال مایع برای کالیبراسیون آن استفاده می شود حدود 10 سانتی متر به عمق فروبری بیشتری نیاز است (15D+SL).
برای جمع بندی دستاوردهای نمودار شکل های 2و3 را می توان در جدول زیر خلاصه کرد:
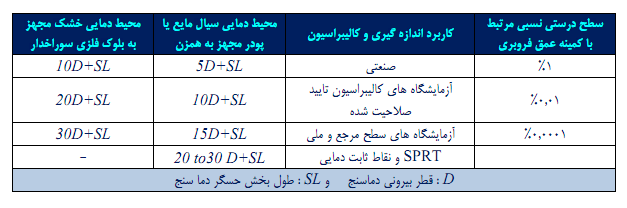
ب) موقعیت و طول بخش حسگر دماسنج
یکی دیگر از مسائل دربرآورد کمینه عمق فروبری ، طول و موقعیت قرارگیری بخش حس کننده دماسنج است که بندرت واقعا درنوک دماسنج و با طول قابل صرف نظر قرار می گیرد. در اینحالت بایستی با دسترسی به اطلاعات طراحی و ساخت دماسنج یا هر روش مناسب دیگری ، محل و طول بخش حسگری در دماسنج را به درستی تعیین کرد و آنرا به طول عمق فروبری تعیین شده براساس معادله مزبور یا نمودار شکل 2 یا 3 اضافه کرد.
پ ) استفاده از غلاف های متعدد ، تودر تو و یا چاهک دمایی
مسئله دیگر دربرآورد کمینه عمق فروبری ، وقتی است که از غلاف های متعدد ،تودرتو یا چاهک دمایی در محل نصب دماسنج برای محافظت آن استفاده می شود و تعیین قطر دماسنج را با مشکل روبرو می کند.
معمولأ استفاده از چاهک های دمایی در کاربردهای صنعتی بسیار متداول است و آنها را در بدنه کوره ها یا سایر ماشین آلات نصب می کنند تا بتوانند دماسنج های صنعتی را در آنها فروبرده و برای اندازه گیری دما یا حتی برای انجام مقایسه و ارزشیابی درستی دماسنج های نصب شده دیگر استفاده کنند. معمولأ این چاهک های دمایی دارای نسبت 5 به 1 برای نسبت طول به قطر بیرونی دارند و برای اندازه گیری های بادرستی اسمی حدود 1% طراحی شده اند. چون چاهک های دمایی کاملأ در بدنه و داخل کوره ها یا ماشین آلات نصب می شوند و دماسنج ها کاملأ درآنها فروبرده می شوند ، تماس آنها با محیط پیرامون و بیرون کمتر می باشد و می توان فرض کرد ضریب K این سیستم کمتر از 1 می باشد. درعوض فاصله هوایی بین دماسنج و چاهک دمایی و همچنین شرایط محیط خشک دمایی و بدون همزن، قطر موثر (Deff) آن بزرگتر از قطر دماسنج (D) خواهد بود. در خوشبینانه ترین حالت دراین سیستم ها ، توصیه می شود قطر موثر (Deff) رابرابر قطر بیرونی چاهک دمایی (ونه قطر دماسنج) در نظر گرفت و کمینه عمق فروبری را تعیین کرد.
یک راهکار دیگر که برخی منابع در تمامی موارد ، هرجا که مشکوک به خطای فروبری است توصیه می کنند ، تغییر و افزایش طول عمق فروبری به اندازه یک برابر یا دو برابر قطر دماسنج و مشاهده تغییرات در دمای خوانده شده است. به صورت تقریبی ، با افزایش هر بار عمق فروبری به اندازه یک برابر قطر موثر ، حدود 60% خطای کل فروبری کاهش پیدا می کند.
مثال :کالیبراسیون یک دماسنج مقاومت پلاتینی (PRT) در حمام مایع مجهز به همزن در آزمایشگاه کالیبراسیون
یک دماسنج مقاومت پلاتینی که قطر 4 میلی متری دارد و موقعیت قرارگیری بخش حسگر آن در40 میلی مترانتهای آن قرار گرفته است، برای کالیبراسیون در حمام سیال مایع مجهز به همزن قرار می گیرد . کمینه عمق فروبری مورد نیاز برای دستیابی به خطای فروبری کمتر از 0.01 درجه سلسیوس تا بیشینه دمای 100 درجه سلسیوس تعیین کنید. فرض کنید دمای محیط 20 درجه سلسیوس است.
حل : ابتدا بهتر است خطای نسبی فروبری راحساب کنید:

با مراجعه به نمودار لگاریتمی شکل 2 (Deff=D)، کمینه عمق فروبری کمی بیشتر از 9 برابر قطر موثر است. برای اطمینان بیشتر بهتر است دماسنج را به اندازه 10 برابر قطر به علاوه طول بخش حسگری آن ، در حمام مایع مجهز به همزن یعنی 80 میلی متر فروبرد:

مثال : کالیبراسیون یک ترموکوپل نوعی با یک محیط دمایی خشک قابل حمل
برای کالیبراسیون یک ترموکوپل با قطر 8 میلی متری در دمای 500 درجه سلسیوس از یک محیط دمایی خشک مجهز به بلوک فلزی سوراخ دار (چاهک) استفاده می شود . دمای محیط پیرامون 22 درجه سلسیوس است. اگر بخواهیم بیشینه خطای مرتبط با هدایت ساقه و عمق فروبری ترموکوپل در دمای حدود 500 درجه سلسیوس ، 0.5 درجه سلسیوس باشد ، کمینه عمق فروبری مورد نیاز را حساب کنید:

با مراجعه به نمودار لگاریتمی شکل 3 (Deff=2D) ، کمینه عمق فروبری بدست آمده از روی نمودار بازای خطای نسبی حدود 0.1% ، 14 برابر قطر دماسنج تحت کالیبره اضافه بایستی باشد. البته با توجه به این نکته توجه داشت که ازطول بخش حسگر ترموکوپل بدلیل کوچکی نقطه اتصال دمایی گرم آن صرف نظر می شود.

نکته : مطابق آنچه در پیوست مدرک معتبر بین المللی منتشره از طرف BIPM در خصوص مقیاس بین المللی دما ITS-90 آورده شده ، معمولآ عمق فروبری مورد نیاز برای کالیبراسیون حسگر های دمایی از دمای محیط پیرامون تا دمای حدود 400 تا 500 درجه سلسیوس افزایش پیدا می کند و پس ازآن به علت اینکه انتقال حرارتی شعاعی بواسطه هدایت حرارت تابشی بسرعت افزایش پیدا می کند ، کمینه عمق فروبری کاهش جزئی پیدا می کند و دلیل آن را هم غالب شدن انتقال حرارتی از طریق پدیده تابش حرارتی در مقابل هدایت حرارتی از طریق ساقه دماسنج می داند . با مدنظر قراردادن این نکته، می توان این کمینه عمق فروبری را برای کالیبراسیون این ترموکوپل در دماهای تا بیش از 1000 درجه سلسیوس نیز مورد استفاده قرار داد.
بخش چهارم ) روش اجرایی تعیین کمینه عمق فروبری و ارزشیابی خطای هدایت ساقه
برای تعیین اینکه آیا خطای هدایت ساقه معنادار است در وحله اول به یک منبع دمایی یکنواخت و پایدار دمایی نیاز است. همچنین درصورتی که با اندازه گیری مشخص شود که گرادیان محوری (و بعبارت دیگر یکنواختی دمایی محوری) یک محیط دمایی کالیبراسیون به اندازه کافی مناسب است ، پس ازآن می توان با اطمینان برای آزمون و ارزشیابی خطای هدایت حرارتی ساقه اقدام کرد . درصورتی که محیط دمایی کالیبراسیون خطای گرادیان دمایی محوری با معنا داشته باشد ، تفکیک گرادیان محوری از اثرات هدایت حرارتی ساقه دشوار خواهد بود و درنتیجه گرادیان های دمایی معنادار در منبع دمایی، نتیجه ارزشیابی سهم عامل هدایت ساقه را بی اعتبار خواهد کرد.
نکته : برای درک بهترو آشنایی با نحوه ارزشیابی گرادیان محوری به مطۀب منتشره دیگری از همین نویسنده درخصوص یکنواختی محوری وحیط های دمایی مراجعه نمایید.
برای بررسی و تعیین کمینه عمق فروبری روش های بسیاری با مفهوم مشترک توسط راهنماهای معتبر بین المللی یا مقالات و مطالب منتشره توسط سازندگان معتبر پیشنهاد شده است. معمولأ دراین راهنماها بصورت کامل درخصوص تعیین مشخصه های اندازه شناسی محیط های دمایی مانند پایداری ، یکنواختی (محوری و شعاعی) و همگنی دمایی ، پسماند و اثر بارگذاری ، روش اجرایی اندازه گیری و نحوه ارزشیابی سهم عدم قطعیت آنها ارائه می شود ، ولی از ارائه روش اجرایی خیلی کامل همراه با ارزشیابی سهم عدم قطعیت عامل هدایت ساقه و عمق فروبری اجتناب می کنند و آن را به عهده مشتری موقع استفاده می گذارندو به همین دلیل سهم عامل هدایت ساقه یا عمق فروبری در بودجه عدم قطعیت کالیبراسیون محیط های دمایی آنها گنجانده نمی شود.
در این بخش از مطلب سعی شده است ، روش های پیشنهادی در استانداردها وراهنماهای بین المللی اندازه شناسی و مطالب و مقالات سازندگان معتبر بصورت جمع بندی شده ارائه شود که عبارتند از:
- روش پیشنهادی شرکت Fluke بخش Hart Scientific
- روش ASTM برای تعیین کمینه عمق فروبری (ASTM D7962)
- روش ASTM برای تعیین کمینه عمق فروبری دماسنج های مقاومتی صنعتی (ASTM E644)
- راهنمای کالیبراسیون کالیبراتورهای دما مجهزبه بلوک های سوراخدار (Euromet /cg-13)
الف ) روش پیشنهادی شرکت Fluke بخش Hart Scientific
روش زیر ، توسط شرکت Fluke بخش Hart Scientific در مقاله " مشکلات مشترک دردستیابی به بیشینه عملکرد کالیبراتورهای دمایی خشک سوراخدار" برای تعیین کمینه عمق فروبری پیشنهاد شده است.
آزمون ارزشیابی خطا و عدم قطعیت اثرات هدایت ساقه بسیار شبیه به آزمون ارزشیابی گرادیان محوری است و کلیات مراحل اجرایی این آزمون در هر نقطه تثبیت شده دمایی در بازه دمایی مورد نظر به صورت زیر است:
- دماسنج مرجع و دماسنج تحت آزمون با وسیله اندازه گیری استانداردی که قدرت تفکیک و درستی کافی برای قرائت دما یا سیگنال متناسب آن را دارد پایش می شوند ،
- دو دماسنج مزبور در کف چاهک محیط دمایی خشک با قطر و عمق مناسب قرار داده می شوند ،
- محیط دمایی خشک در دمای مورد نظر تنظیم و به دماسنج ها مهلت داده می شود تا به تعادل دمایی برسند ،
- اختلاف بین مقادیر دمایی دو دماسنج ثبت می شوند (اختلاف دمایی اول) ،
- دماسنج تحت آزمون به اندازه 10 میلی متر از کف بالا برده می شود و مهلت کافی برای برقراری تعادل دمایی داده می شود،
- اختلاف بین دو دماسنج مجدد یادداشت و این دو اختلاف ارزشیابی می شوند. اختلاف اول برای حالتی است که دو دودماسنج در کف چاهک قراردارند و اختلاف دوم برای حالتی است که دماسنج مرجع هنوز در کف چاهک قراردارد ولی دماسنج تحت آزمون به اندازه 10 میلی متر بالا برده شده می باشد ،
- اگر این دو اختلاف دمایی زیاد باشد نشانگر اثر قابل ملاحظه هدایت حرارتی ساقه یا همان خطای عمق فروبری است و در صورتیکه تغییر معناداری بین این دو اختلاف مشاهده نشود، می توان استنتاج کرد که خطای هدایت حرارتی ساقه کوچک است،
- ارزشیابی این اختلاف دمایی را ادامه داده و هربار دماسنج تحت آزمون را به اندازه 10 میلی متر نسبت به موقعیت قبلی بالا برده و اختلافات دمایی در هر موقعیت جدید را یادداشت کنید. بدیهی است هرچه دما سنج تحت آزمون به سطح بالایی چاهک نزدیک شود ، به دمای محیط بیرونی نزدیکتر خواهد شد. هرچه این نزدیک شدن به دمای محیط سریعتر باشد، نشانگر خطای بزرگتر برای هدایت ساقه و عمق فروبری است و برعکس هرچه این سرعت کمتر باشد نشانگر خطای کوچکتر است.
شکل 4 بصورت نوعی ، مقایسه ای از اثر عمق فروبری برروی دماسنج ها با ساختار متفاوت دارد که در دمای حدود 420 درجه سلسیوس در یک محیط کالیبرسیون خشک با عمق چاهک 20 سانتی متری در مطالعات انجام شده توسط شرکت Fluke است. در صورتیکه دماسنج های مرجع و تحت آزمون یا کالیبراسیون ساختار یکسان داشته باشند ، خاصیت کسب یا اتلاف حرارتی آنها مشابه خواهند بود و درنتیجه خطای هدایت ساقه و عمق فروبری به حداقل خواهد رسید .
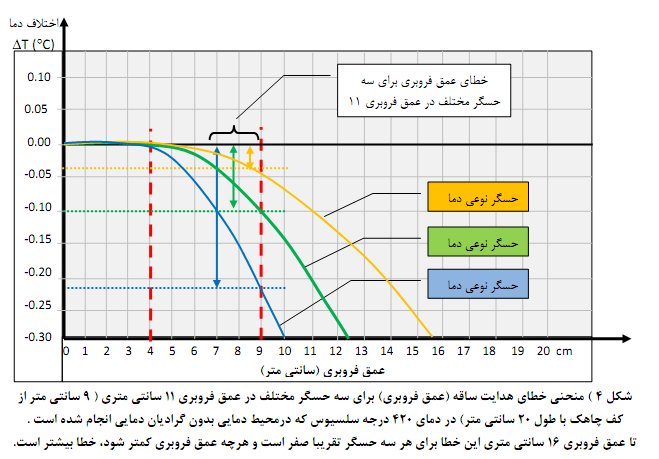
ب ) روش ASTM برای تعیین کمینه عمق فروبری (ASTM D7962)
استاندارد ASTM D7962 دربرگیرنده روشی برای تعیین کمینه عمق فروبری برای حسگرهای دمایی به ویژه انواع دماسنج های مقاومتی (RTD[18]) یا حسگرهای مشابه است و شامل مراحل اجرایی زیر است:
- قبل از شروع به اجرا، لازمست از پایداری دمایی محیط دمایی مورد استفاده و سازگاری درستی وحساسیت دستگاه های اندازه گیری دما و ملحقات آن با عدم قطعیت اندازه گیری دمایی مشخص شده
- فاصله بین نوک حسگر نسبت به علامتی مرجع روی ساقه، غلاف یا هرنقطه مرجع دیگری را اندازه گیری نمایید،
- محیط دمایی بطور مثال حمام نقطه یخزدگی [19] آب یا یک حمام با دمای ثابت و همگن شده را آماده کنید،
- پس از اطمینان از تثبیت و همگنی دمایی حمام ،به آرامی آنقدر دماسنج را داخل حمام فروبرده تا با هرگونه فروبری بیشتر تغییر معناداری در دمای خوانده شده یا سیگنال خروجی حسگر مشاهده نشود. فروبری دماسنج می تواند دربرگیرنده فروبری فلنج نگهدارنده ، پیچ و سایر ملحقات آن نیز باشد. بایستی توجه داشت که شرایط محیطی تاثیر بیشتری برروی دم آنچه درمورد صنعت نسل 4 (Industry 4.0) یا انقلاب صنعتی چهارم بایستی دانست...
ما را در سایت آنچه درمورد صنعت نسل 4 (Industry 4.0) یا انقلاب صنعتی چهارم بایستی دانست دنبال می کنید
برچسب : نویسنده : calibration-info بازدید : 124 تاريخ : سه شنبه 7 تير 1401 ساعت: 6:56